The decision to build a website or a complex software application is a major inflection point for any business. But the real critical decision isn't about features or color schemes; it's about who will build it. Do you assemble an in-house te
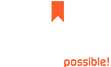
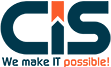
The decision to build a website or a complex software application is a major inflection point for any business. But the real critical decision isn't about features or color schemes; it's about who will build it. Do you assemble an in-house te
Managed IT services (MIT services) are IT tasks outsourced by businesses to service providers known as managed IT service providers (MSPs). Through annual or monthly subscription a
Hey there, tech leaders and innovators. Let's talk turkey. Your web platform is the heart of your business, but keeping that heart beating strong in today's chaotic tec
When hiring from staffing providers or outsourcing firms, your initial step should include interviewing candidates that meet your criteria for team members that best suit your needs and integrate into your internal team while upholding company cultur
In a world where speed is king, your smartphone has become your wallet. With a simple tap, you can buy coffee, pay for groceries, or breeze through transit gates. This magic is pow
Not only would that attract new clients, but it would establish your authority in the field and even build upon current business relationships by building upon those already there.
Although convenient, public WiFi isn't necessarily secure. We explain the methods used by cybercriminals and show you how to always be one step ahead. Free Internet access at any time and from any location is quickly becoming the norm rather than
HR software is the digital solution to managing and optimizing human resources and meeting organizational goals. The HR software allows managers and HR staff to allocate time and r
Offshore software development has emerged as a strategic approach for businesses looking to enhance their technological advancements capabilities while optimizing costs. According
In today's digital landscape, in the year 2025, the projected revenue in the Application Development Software market worldwide is expected to reach a staggering US$195.80bn. No
The role of HRMS and HCM software has evolved far beyond mere record-keeping or payroll management. In the digital age, these systems have become indispensable for businesses aimin