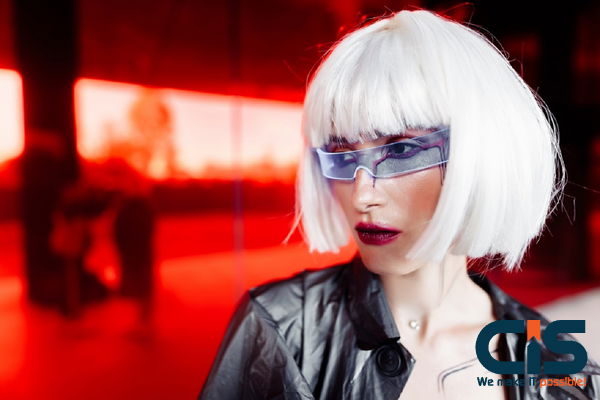
Internet of Things technology has become essential in manufacturing's dynamic environment. Industry 4.0's technological innovations make businesses more innovative, adaptive, and resilient; from wearable devices to 3D printers - IoT applications in manufacturing offer significant returns.
- smart home devices
- connected devices
- human intervention
- physical devices
- internet connectivity
- internet-connected devices
In this blog, we will cover eight IoT applications used in manufacturing. In addition, we'll examine future trends that may revolutionize this sector - let's dive deeper into the IoT world in manufacturing!
IoT Growth
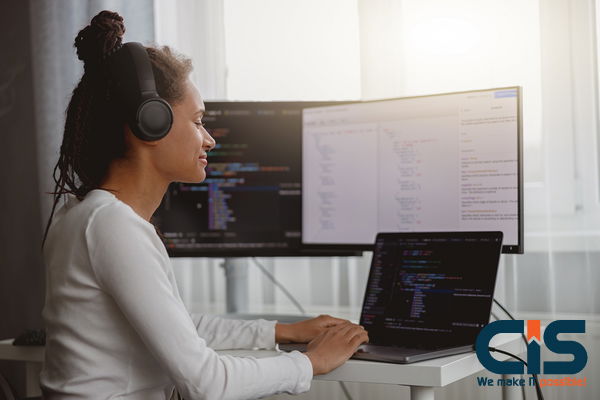
The Internet of Things is experiencing exponential growth due to factors like predictive maintenance, increased production efficiency, and streamlining the management of manufacturing infrastructure. Manufacturers using IoT gain greater control and visibility into production as it transforms manufacturing through optimization of production, reduced downtime, predictive maintenance, and optimized scheduling of spare parts replacement.
Here are just a few ways the IoT could simplify and enhance your manufacturing processes:
- Manufacturers can utilize data gathered from machinery and equipment in their factories to analyze trends better and pinpoint areas for improvement.
- Real-time production monitoring and key performance indicators can be easily monitored using this software system, with easy replication, audits, and prompt resolution for production-related issues.
- This technology connects wireless machines directly to the internet, enabling manufacturers to monitor and manage their equipment from any location remotely, increasing efficiency while decreasing downtime.
- IoT-enabled devices can collaborate and exchange information for more coordinated and efficient production processes.
- IoT technology can assist manufacturers in minimizing unscheduled downtime, increasing productivity, and avoiding potential problems.
Predictive Maintenance
Predictive maintenance is one way to avoid equipment breakdowns or failure. IoT makes predictive maintenance all the more valuable; connected machines enable data collection in real-time so issues can be identified before causing disruptions in operations.
IoT-enabled predictive monitoring sensors enhance manufacturing safety, reduce costs, and enhance quality. Wireless predictive maintenance sensors can measure machines' vibrations, temperature, speed, motion, and sound acceleration to assess whether they're operating normally.
- fitness trackers
- device management
- energy usage
- massive amounts
- self-driving cars
Temperature sensors are ideal for measuring temperature in industrial boilers and liquid storage containers and provide accurate readings in all temperatures. Incorporating various measurements makes for optimal use when measuring industrial temperatures such as:
IoT sensors allow manufacturers to anticipate potential downtime, taking steps to address it quickly. Wireless industrial sensors help increase safety by anticipating when machines may explode or be unsafe, thus helping ensure business operations run as efficiently and safely as possible.
Asset Tracking And Location
The large amount of assets that need to be tracked makes asset tracking difficult. It isn't easy to track investments because they are constantly moving. It can result in damaged or costly investments.
Quality Management
Monitoring all factors that contribute to product quality is part of any quality management program, from controlling temperature, humidity, and air quality through controlling temperatures to keeping humidity under control for manufacturing plant products. Humidity control, in particular, can prevent various manufacturing issues like:
Quality assurance was traditionally conducted manually and subject to error; however, with IoT, manufacturers can monitor more precisely parameters like temperature, humidity, and pressure using sensors collected through IoT devices - essential when meeting ISO or GMP regulations.
Warehouse Management
Logistics refers to coordinating, controlling, and organizing products, equipment, and materials in manufacturing environments. Due to rising costs and complex requirements of modern production lines, modern production relies heavily on logistics management services for product control.
Companies spend millions upgrading their capabilities; unfortunately, these investments don't always yield positive returns due to not meeting industry challenges adequately. Logistics poses particular difficulties.
Management and control of product deliveries are challenging. Order processing times become problematic. Due to globalization and increased production complexity, faster deliveries may occur with shorter lead times and travel times for carriers.
- application layer
- vast amounts
- IoT Analytics
- communication between devices
- wearable technology
- edge computing
- Google Home
Due to increasing fuel costs, companies must find ways to cut transport expenses wherever possible. Warehouse layout inefficiencies, tracking inventory levels, and controlling goods movements all present manufacturing industries with unique challenges that must be managed effectively for continued operations.
Use Iot Case When Traveling
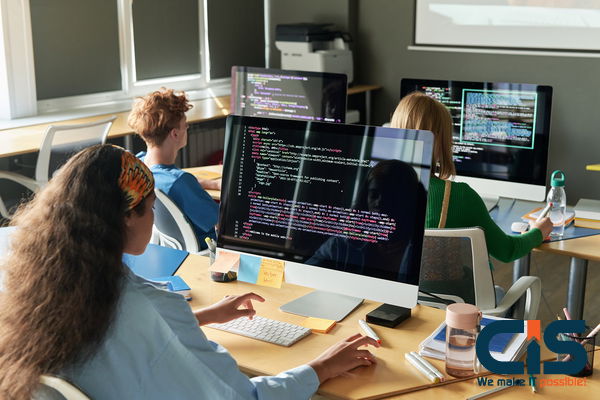
Internet of Things and Workplace Safety
IoT plays an increasingly critical role in workplace safety. Safety leaders use IoT to move and secure employee safety information more efficiently. In contrast, its use by teams allows quick detection and prevention measures, ultimately significantly lowering claims related to non-compliance costs.
Preventing Future Problems
Manufacturing companies face difficulty identifying anomalies or malfunctions in machines that cost too much to fix quickly and cost the business financially. IoT sensors embedded into machines can help monitor their current state using Predictive maintenance (or condition-based maintenance). With this setup, monitoring machine failures or abnormalities is straightforward, while creating maintenance schedules using AI-powered analytics or machine learning is effortless - as are cost savings, too!
Asset Tracking
IoT technology can help manufacturing companies track assets. Staff often struggle to track assets in real time and misplace information. Attaching IoT-enabled devices directly to storage containers makes identifying assets easy, while other technologies such as RFID or NFC offer accurate purchase identification that allows employees real-time updates; all this technology saves both time and money for manufacturing firms.
Maintain Inventory with IoT
An inventory management system implemented within manufacturing. Locating products within large warehouses is time-consuming and difficult; IoT devices such as sensors simplify the task by making tags to make materials easier to locate in large spaces like this one, thus saving both money and time! This system makes finding anything quickly within large spaces more manageable while saving both.
Product Quality IoT
Quality issues can significantly hamper a company's financial and brand performance, rendering simple observations insufficient in measuring production quality. IoT devices allow manufacturers to track the production process as it evolves; using real-time monitoring data collected via sensors they collect, IoT can monitor production progress while at the same time improving quality control processes and increasing productivity.
Product Tracking with IoT
Tracing product movements and identifying their locations is no simple task, which may delay project delivery. IoT-enabled devices make it simple for manufacturers to monitor an assembly line in real-time, saving them money and time as they witness products delivered quicker to market.
Leading manufacturing firms are turning to IoT technology to monitor machine performance and predict equipment breakdown, leading to increased productivity and reduced maintenance costs.
Want More Information About Our Services? Talk to Our Consultants!
The IoT Industry
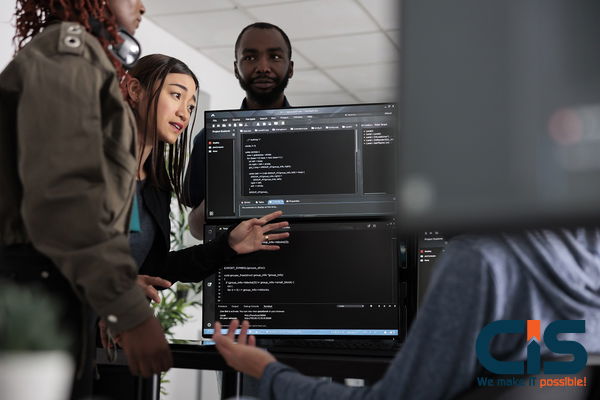
The Industrial Internet of Things is an essential step toward modernizing factories into intelligent spaces, disrupting traditional factory workflows by increasing productivity, efficiency, and employee safety - not to mention millions saved! Check out some eye-opening statistics!
Industry 4.0 has made its presence felt in manufacturing. Smart manufacturing is becoming an increasingly important trend that manufacturers eagerly embrace to move towards more intelligent and interconnected production systems.
How Will The Internet Of Things Influence Industrial Manufacturing?
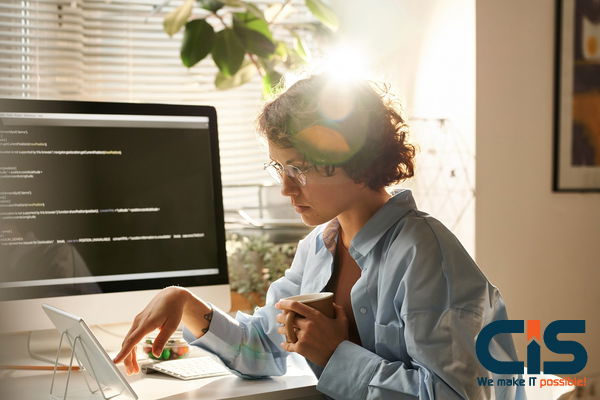
Industrial manufacturers have faced complex efficiency issues for years. When faced with competition from manufacturing rivals, many organizations had to expand into new markets or improve efficiency to remain viable. The IoT may help manufacturers address some of these challenges head-on by seamlessly connecting all aspects of production networks - which means less downtime during operations!
Savings may not be generated in an ecosystem that relies heavily on an international network of distributors to maintain and sell its products; there's often little opportunity to make additional money off initial purchases; investors don't like seeing price wars happen as their investment doesn't offer hope of revenue growth once the products become commoditized.
- medical devices
- vital signs
- supply chain management
- technology stack
- Google Nest
- wireless connectivity
- sensor technology
To remain competitive in today's globalized world, industrial manufacturing firms need to adjust their strategy and cost structure dramatically. IoT can assist industrial manufacturing firms by collecting and transmitting data throughout the manufacturing process - sensors can gather this information at one central point from factory floors to end product - which then can be analyzed for actionable insights.
IoT provides more than process enhancement in the factory; it can offer greater insight into operations on the factory floor for increased efficiencies that include personnel optimization, fuel and environmental savings, and increased automation.
The electronics plant in Germany provides an outstanding example. Automated machines and computers control 75% of value chains; around 1000 automation controllers work end to end; parts communicate using product codes so machines know precisely what parts to order next; processes are optimized for IT control, resulting in lower failure rates, while employees oversee technology assets while managing unexpected incidents that arise during production.
Industrial Iot Manufacturing: From Product To Service
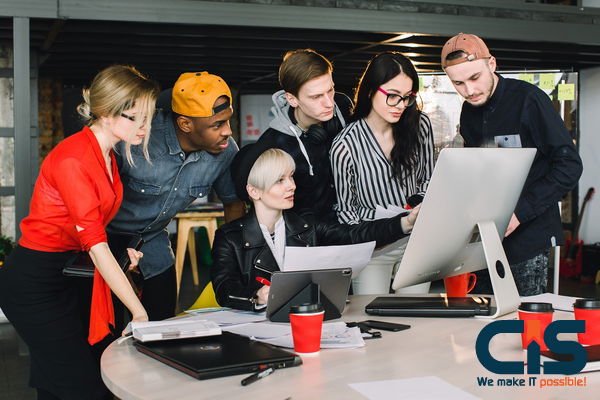
Deployments have helped companies significantly transform their businesses through industrial manufacturing deployments. Businesses are making crucial adjustments in their digital strategy in preparation for the digital economy; innovation will play a central role in creating one.
Despite early stages and ongoing developments, The Aberdeen Group finds evidence of strong commitment among manufacturers towards digital transformations. 35% intend to transform their businesses with digital technology; 91% consider IoT benefits to be positive additions to manufacturing operations.
Industrial manufacturers will benefit significantly from using Internet of Things 4.0 technology for monitoring factory machines, but also as part of an innovative sales and service offering, for instance, selling excavators. Such an approach helps industrial manufacturers differentiate themselves while helping avoid the commoditization of products or services offered to clients.
Not to underestimate this transformation process is critical; scaling from traditional sales via a distributor to direct service delivery can be daunting, especially as customer purchasing habits shift away from CAPEX to OPEX purchases. Most organizations elect for gradual implementation of IoT as this marks their digital journey's infancy.
The IoT and Manufacturing Industry
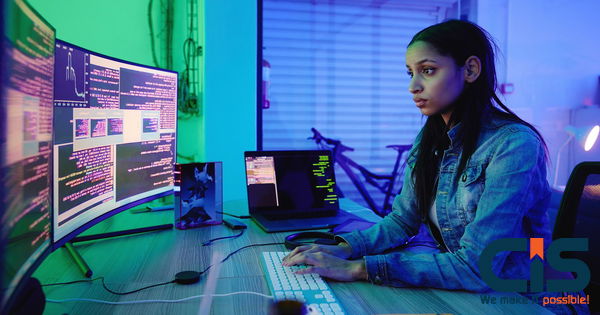
IoT and manufacturing The digital revolution has transformed manufacturing. Innovative technology is being leveraged by businesses to transform their eco-systems; research studies reveal digital leaders adopt game-changing solutions related to Industry 4.0 solutions; digital success stories are inspiring today; here is an overview of how IoT has transformed this industry sector.
Early Warnings of Malfunctions
According to one analyst's firm, unplanned downtime costs businesses up to $260,000 an hour in terms of lost production time or machine damage costs alone, as Manufacturing Companies Association International reported. IoT gadgets utilize sensors that monitor temperature, vibrations, and voltage-current levels in real time, allowing these gadgets to detect early warnings of malfunction and provide safer working environments for frontline workers.
Increased Margin and Customer Satisfaction
IoT products and services offer manufacturers exciting possibilities, from increasing margins and customer satisfaction to strengthening client relationships through remote diagnostics that improve service. Remote diagnosis increases customer satisfaction while cutting repair times and strengthening client relationships through creating stronger ties - creating stronger bonds over time with them all. Early warning signals or detection could enhance quality while simultaneously offering customers a more satisfying service that receives higher marks overall.
A Connected Supply Chain Improves Asset Management
Customers now expect more from manufacturers, with faster delivery times as one of the significant criteria they evaluate when choosing service providers. Manufacturers have responded by exploring micro-logistics as one solution to meet accelerated delivery needs. At the same time, IoT at the asset level in connected supply chains provides inventory visibility, allowing a better overview across logistics networks.
Implement Operational Intelligence
According to experts, autonomous machines will gradually replace manual labor with interconnected robot networks that communicate and coordinate independently without much human involvement.
Enhancing Quality
IoT sensors gather information about product specs and metrics and third-party input at various stages in its life cycle, giving manufacturers insight into which items need physical inspection or require further adjustments to comply.
Information collected about raw materials used, transportation effects, and other variables influencing final products are collected via IoT systems such as those created by manufacturers; as an added feature, they provide insight into consumer reactions that help identify and address quality issues more quickly and easily.
Better Production Planning and Scheduling
Companies using IoT-based solutions for manufacturing can experience enhanced production planning and scheduling capabilities due to IoT, benefitting product quality and yield. Manufacturing firms experience more effective production scheduling, better planning of production operations, and real-time visibility into production operations. Consider, for instance, your company requires more than 100 inspections each week that consume 20% of production costs - automating quality controls can transform this situation drastically.
Better Plant Safety and Security
IoT and data analytics can dramatically enhance plant safety and security by tracking KPIs such as vehicle accidents, employee absences, and injuries. IoT technology also offers real-time insight into these critical areas so issues can be dealt with immediately while manufacturers ensure compliance with environmental health and safety regulations.
Security concerns surrounding IoT technology have long been of great concern; hackers have exploited it to access company data easily. There is growing dissatisfaction about different security protocols used across suppliers and an absence of standardization among these protocols; as a way of combating security problems, operational technology must work hand-in-hand with IT.
Use Cases For Iot In Manufacturing
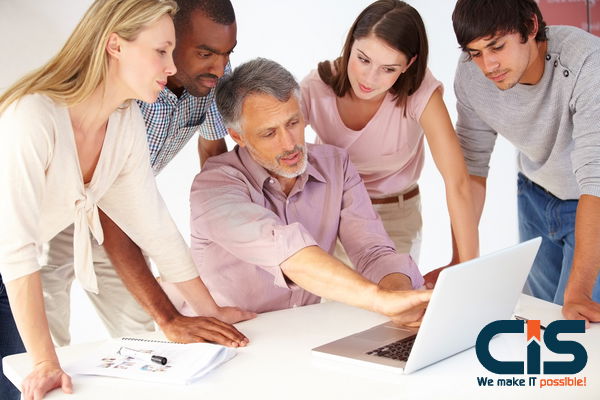
Remote Monitoring
Industrial leaders who own assets that can be connected through IoT should recognize the significance of remote monitoring as a practice to assess performance. IoT sensors monitor equipment health and usage patterns for accurate performance evaluation and deployment support if issues arise with services provided to their clientele.
Armal, a manufacturer of portable restrooms, uses molding equipment to produce plastic components and frames for their products, with power monitoring to optimize and monitor the consumption of their machinery. The model offers new opportunities in terms of the Equipment-as-a-Service business model. For instance, for Armal to succeed, they needed an optimal and monitored energy consumption structure within their machinery fleet.
- access control
- remote controls
- Smart grids
- vast amounts
- Amazon Echo
Armal can remotely monitor energy use for their production with Internet of Things sensors and software, helping reduce energy costs by nearly 40%. At the same time, the digitization journey was concluded, with Armal purchasing an IoT solution to monitor each machine in real-time power usage monitoring solutions.
Digital Twins
Digital twin technology has gained increasing attention. According to IDC estimates for 2018, companies investing in this IT form may expect a 30% improvement in critical process cycle times using Digital Twin technology. Leaders combining IoT with their Digital Twin can use an in-depth assessment. Some technologies that use Digital Twins include Cloud Services, IoT/Extended Reality Platforms/AI.
Companies using IoT (also referred to as Digital Twins) can create robust virtual copies and digital replicas of objects for use on production floors, where managers can utilize virtual spare part replicas in simulation processes or troubleshooting without risking physical assets or risking destruction or degradation of physical assets.
Air Products Inc., a producer and provider of compressed air products, implemented Digital Twin Technology to move away from selling physical products towards providing services. Their Digital Twin System provided operational data such as the air consumption rate.
Success billing its clients according to air consumption instead of charging flat rates, thus significantly cutting commodity costs by 30 percent and signing on nearly half of the significant vendors as clients.
Logistics Management
Manufacturing firms face numerous logistical risks when managing weather-dependent logistics operations. Fraud and the sheer volume of assets to oversee are further contributing factors, so IoT interconnections may provide valuable assistance in maintaining efficient workflow for transport-dependent firms.
Applications for IoT in Logistics can address multiple use cases across supply chains - from warehousing and fleet management, cargo tracking, and asset inventory to cargo tracking and security monitoring. IoT technology serves as the backbone for digital transformation efforts.
Amazon benefits greatly from drop-shipping bots; these delivery robots enhance delivery convenience while making money, leading manufacturers to enjoy lower shipping costs while automating order processing, status updates, and delivery to reduce the need for extra staff members. When used as last-mile deliveries connected to the internet, bots connected can reduce costs while increasing customer satisfaction and loyalty. Logistics managers can utilize IoT technology to reduce fuel and repair costs while improving driver safety and decreasing inventory damages and insurance premiums. Tasks they complete could include monitoring fuel prices, smart delivery drivers, diagnostics testing of vehicles or drivers, and real-time monitoring of vehicle and driver performance - with real-time monitoring providing further improvements such as technician safety increases and decreased inventory damages or insurance costs.
Manufacturing Key Performance Indicators
(KPIs), also referred to as KPIs, provide vital insight into a business's performance. Manufacturers rely on KPIs as quantified measurements that help focus their company's activities and track, analyze, and optimize performance. One of the more frequently utilized manufacturing KPIs is overall equipment efficiency (OEE). OEE measures performance, availability, and quality at factories. While OEE may accurately reflect factory operations, other KPIs should also be utilized to understand how performance may change over time.
Manufacturers in the manufacturing industry can select from an assortment of KPIs that will guide their decision-making, such as KPI dashboards. A KPI dashboard helps keep company priorities front of mind and can ensure your organization remains on course.
Dashboards, analytics, and reports all play an integral part in understanding an organization's performance; time is critical to assess whether performance meets expectations. Industrial IoT platforms help compile and contextualize data that produces user-friendly dashboards and reports that display its status.
Read More: Internet of Things (IoT) Security
Trends for IoT in Manufacturing by 2023
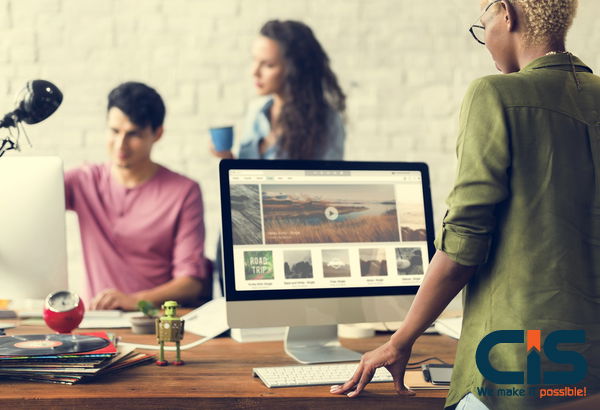
Employee Safety
The National Safety Council (NSC) estimated the annual costs associated with workplace injuries at 171.0 billion dollars. This cost estimate covers wage and productivity loss, medical and administrative expenditures, and uninsured costs, which represent time lost by workers who were either directly or indirectly injured.
Manufacturing industries can be one of the most hazardous fields, with hundreds of accidents annually. The Internet of Things will soon become a trend within manufacturing to prevent injuries and enhance safety; sensors provide accurate information regarding equipment conditions or facilities while simplifying identifying potential dangers and risks. IoT can enhance safety in numerous ways.
- smart devices
- security technologies
- battery-free sensors
- edge gateways
Wearable devices to monitor technicians' blood pressure and heart rates as they work are available, as are devices that detect temperature variations or fire, with intelligent sensors providing alerts when certain levels are exceeded. Fire sensors detect temperature variations or fire, with smart alerting when these thresholds have been breached.
Privacy and Security
IT experts have become more focused on privacy and security. Manufacturing processes pose risks of cyber threats that are of particular concern for IoT users. As traditional factories transition into intelligent factories, data leaks (or malware/ransomware infections) must be carefully addressed to create secure environments for these plants. IoT systems require authentication in all areas - cloud services, software applications, and networks- to protect users. Here are ways of safeguarding IoT ecosystems such as these: Implementing security and awareness into corporate culture is crucial.
M2M Automation
M2M was first adopted within manufacturing and industrial environments where SCADA, remote monitoring, and other technologies allowed remote management and control of equipment data. M2M transmits sensor information directly from sensors onto computer networks for data transmission and processing.
Intelligent sensors embedded into devices enable communication. IoT uses these sensors to automate and communicate decisions related to materials procurement, sales forecasting, and distribution without human interference. Integration of M2M data with enterprise software is vital for manufacturers who seek to take full advantage of automation. ERP allows machines and products to communicate, allowing technicians to monitor production closely. There are various uses for M2M technology:
Blending IoT With VR/AR to Connect Digital and Physical Worlds
VR and AR provide significant economic benefits when combined with IoT data, including increased profits, lower costs, new product/service opportunities, and many others. 2023 will see continued IoT development; these use cases illustrate its relationship with AR/VR applications and IoT.
Equipment Management
Data gathered by Internet of Things sensors on equipment health is displayed live using virtual elements to show malfunctions or crashes.
Manage Spaces
AR can assist companies and workers alike in optimizing the location and layout of factory inventories and routes so that workers can safely navigate them.
Education of Employees
IoT data can be utilized to build virtual models of machinery or products and simulate them so employees learn the most effective ways to operate them.
Want More Information About Our Services? Talk to Our Consultants!
Wrapping up
Intelligent solutions enable manufacturers to remotely oversee, control, and manage all aspects of their facility - production, inventory, and maintenance management included - from Production through Maintenance to Downtime reduction and increased operational efficiencies.
Manufacturers looking to leverage IoT must first be confident their data is secure under their complete control, and interoperability between systems is critical in realizing its full benefits. Over time, as your ecosystem matures, further value will accrue - using these devices can help manufacturers stay ahead of competitors while expanding bottom and bottom lines.
IoT in manufacturing presents promising growth prospects. Many leading companies are investigating ways IoT technologies can take full advantage of digitization to drive savings while creating excellence in production. The potential applications include improving process control and monitoring data analytics in production settings.