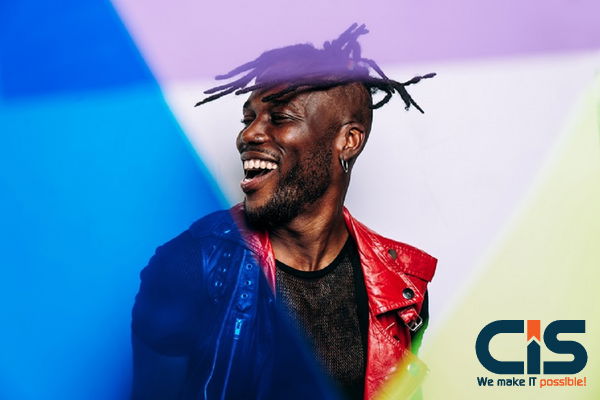
Understand Maintenance Strategies
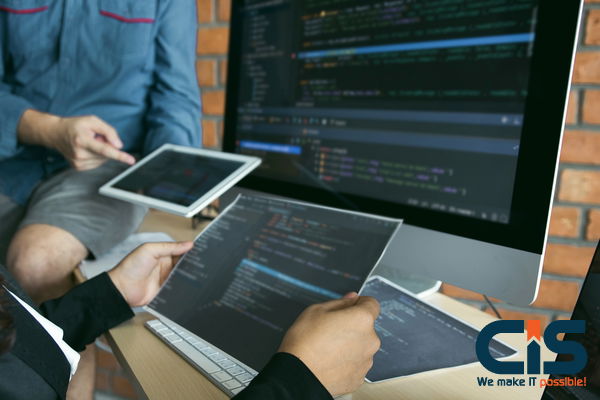
Maintenance is an essential function for any organization that depends on equipment, machinery, or infrastructure for efficient operation. Maintenance strategies are developed by organizations to ensure these assets operate efficiently and reliably throughout their lifetime. This article will explore what maintenance strategy is, why it's essential, and the different strategies used across various industries.
Want More Information About Our Services? Talk to Our Consultants!
What are Maintenance Strategies?
Organizations use maintenance strategies to optimize, manage, and maintain their assets. These strategies include several processes and methods designed to ensure the longevity, reliability, and availability of facilities and equipment. Maintenance strategies are designed to reduce or eliminate unplanned downtime and operational risk and control costs.
Why are Maintenance Strategies Important?
For several reasons, maintenance strategies are crucial. They are essential in ensuring infrastructure and assets' reliable and efficient operation in different industries. These are the main reasons that maintenance strategies are crucial:
- Reduce Unplanned Downtime: A primary goal of maintenance strategies should be to reduce or prevent unplanned downtime. Equipment failures can cause costly interruptions to production, services, or operations. Maintenance plans allow organizations to address problems before they become problems and maintain continuous operation.
- Cost savings: Effective Maintenance Strategies can result in significant cost savings. For example, preventive maintenance allows an organization to refurbish or replace components before they break down catastrophically. It is more economical to use this approach than expensive emergency repairs and equipment replacements.
- Safety A well-maintained machine is safer both for the employee and the environment. Maintaining equipment in good condition reduces the risks of injuries and accidents caused by failing machinery.
- Compliance Maintenance is a requirement in many industries. Safety, quality, and environmental standards must be adhered to by organizations. Maintenance strategies that are well-planned and implemented can help companies comply with regulations and avoid penalties.
- Asset Durability: Assets constitute a significant investment, regardless of whether it is machinery, vehicles, or infrastructure. These assets are meant to be operated for longer by using maintenance strategies. Regular maintenance helps organizations protect their assets and increase the value of those assets.
- Operational reliability: In industries where equipment performance directly affects production or service provision, reliability is critical. Maintenance programs improve the asset's reliability and ensure that it performs consistently.
- Allocating Resources Efficiently: Maintenance Strategies help organizations distribute resources effectively. Prioritizing maintenance activities according to asset risk and criticality allows organizations to allocate budgets and resources efficiently.
- Better Decision Making: The maintenance strategies are data-driven and analytic. Information collected by equipment, sensors, and performance indicators is used to create these strategies. These data provide valuable insight that helps organizations make better decisions.
- Sustainability Maintenance Strategies can help with sustainability. Maintenance strategies often integrate energy-efficient practices and environmental compliance with responsible resource management. This allows organizations to reduce their environmental impact.
- Customer satisfaction: In service-oriented businesses, reliable maintenance is essential to delivering services as promised. This leads to increased customer trust and satisfaction. Customers can be unhappy with unscheduled failures and disruptions, which could damage an organization's reputation.
- Competitive Edge: Organisations implementing maintenance strategies effectively can have a competitive advantage. Reduced downtime, maintenance costs, reliable operations, and reduced operational interruptions can result in cost savings for the company and improved customer service.
Maintenance strategies are essential because they allow organizations to maintain operational excellence and minimize disruptions. They also help them save money, comply with safety regulations, and safeguard valuable assets. Adopting the right maintenance strategies and constantly refining them can help organizations succeed in their industries and gain a competitive edge.
Maintenance Strategies
Organizations use a variety of maintenance strategies to manage their assets effectively. The systems are broadly classified into:
- Reactive maintenance: This strategy, also known as "breakdown" or "run to failure" care, involves only fixing the equipment when it breaks. It is suitable for assets that are not critical and have low downtime costs. Still, it can become expensive and disruptive when used on equipment, which is crucial.
- Maintenance Preventive: The strategy involves scheduling regular maintenance, regardless of equipment condition. The goal of preventive care is to avoid failures through the replacement or refurbishment of components before they wear out. It can reduce the likelihood of unplanned breakdowns. Still, it may also result in excessive maintenance on equipment in good shape.
- Maintenance Predictive: Data and analytics are used to determine when maintenance on equipment is required. By collecting and monitoring data and continuously monitoring equipment performance, companies can detect wear and tear, degradation, and impending failure and plan maintenance at the right time. This reduces unplanned maintenance and downtime.
- Reliability Centered Maintenance (RCM). The RCM approach prioritizes assets according to their risk and criticality. This involves in-depth analysis to determine the best maintenance strategy for each purchase and optimize resource allocation.
- Total productive maintenance (TPM). The TPM approach is holistic and aims to increase the overall effectiveness of equipment (OEE) through engaging all employees. The focus is eliminating defects and downtime while promoting an ownership culture.
- Condition Based Maintenance (CBM). TO DETERMINE EQUIPMENT HEALTH, the CBM process involves monitoring specific requirements or parameters, like vibration, temperature, or lubrication. The maintenance is performed according to the state of an asset. This ensures that resources are utilized efficiently.
- Run-to-Overhaul (RTO). This is a common strategy in the aerospace sector. The equipment is run until it reaches the predetermined threshold. At that point, it's overhauled, or it can be replaced. The strategy aims to balance the requirement for component reliability and the desire to extend the life of the components.
How to Choose the Best Maintenance Strategy
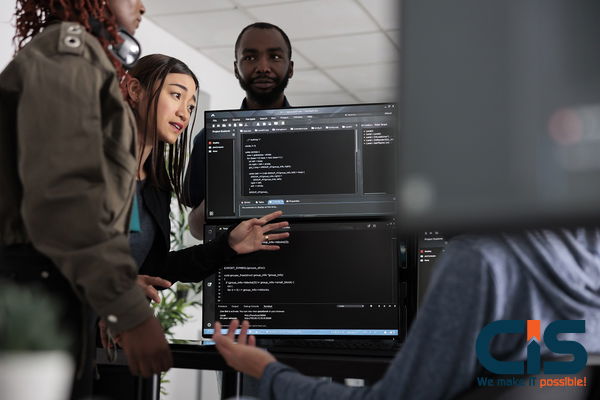
The proper maintenance strategy can directly impact the efficiency and effectiveness of an organization's operations. Maintenance strategies should be chosen according to the goals of an organization, the criticality of assets, the available resources, and the type of equipment or infrastructure being managed. You can use these steps to select the best maintenance strategy.
Asset Criticality Assessment
- Start by categorizing and identifying your assets according to their importance for your business. If you fail to protect your critical assets, it will have an even more significant impact on the industry.
- When determining the criticality of a situation, consider factors like safety, interruptions in production, financial impact, and environmental impacts.
Define Your Goals And Objectives
- Define your goals and objectives for maintenance. Do you want to minimize downtime, reduce costs, increase safety, or reach other outcomes?
- The maintenance plan you choose will be based on your goals.
Understanding The Types Of Maintenance Strategies
- Familiarize yourself with various maintenance strategies, including reactive, preventive, predictive, reliability-centered, total productive, and condition-based maintenance.
- Understanding the advantages and limitations of each strategy.
Assess Resource Availability
- Assessment of the available resources for maintenance, such as personnel, budget, and equipment.
- Ensure you have the resources necessary to implement your maintenance strategy.
Calculate the Complexity of Equipment
- Take into account the complexity of equipment and infrastructure. Certain assets require expert maintenance or specialized techniques.
- Assess if you have the knowledge and skills to use specific maintenance methods.
Data and Technology Analysis
- Assess your data collection capabilities. Data and technology are essential for condition-based and predictive maintenance, which includes sensors and analytics.
- Check if your infrastructure is capable of supporting data-driven care.
Regulatory Requirements
- Remember that specific regulations or standards may apply to your industry and dictate your maintenance procedures.
- To avoid compliance issues, ensure that the maintenance strategy you choose aligns with any regulatory requirements.
Risk Assessment
- Assess the risks that may be associated with each strategy of maintenance. Take into account factors such as reliability, cost, and safety.
- Analyze the impact of each scenario on these risks.
Cost-Benefit Analysis
- Analyze the cost-benefit of each strategy for maintenance. Consider the cost of the implementation and ongoing maintenance, as well as the potential for downtime. Also, consider the benefits of increased efficiency and reduced failures.
- Comparing the cost-effectiveness over time of different strategies.
Also Read: Understanding Software Maintenance Best Practices
Consult Experts
- Ask for input from experts in the field, such as maintenance engineers and professionals.
- They can offer valuable insights into the best maintenance strategies.
Tailor Your Strategy
- Many organizations combine maintenance strategies. Customize your maintenance strategy for each asset. Predictive or condition-based preventive maintenance may be used for critical assets. In contrast, a more proactive approach may be taken with less important ones.
Continuous Monitoring And Adaptation
- After selecting a strategy for maintenance, monitor the effectiveness of that plan.
- Prepare yourself to adjust and fine-tune your strategy in response to performance data and changes in circumstances.
Documentation And Training
- Documentation of your strategy, schedule, and procedures for maintenance.
- Ensure the maintenance staff is adequately trained and knows their role in implementing your chosen strategy.
A systematic and thoughtful approach is required to select the best maintenance strategy. Organizations can align their maintenance practices to operational objectives and needs by considering asset importance, goal, resource availability, complexity, regulatory requirements, and data capability. It is important to remember that selecting a maintenance strategy does not have to be a single decision but instead reflects evaluating and improving the process over time.
How to Choose the Best Maintenance Method
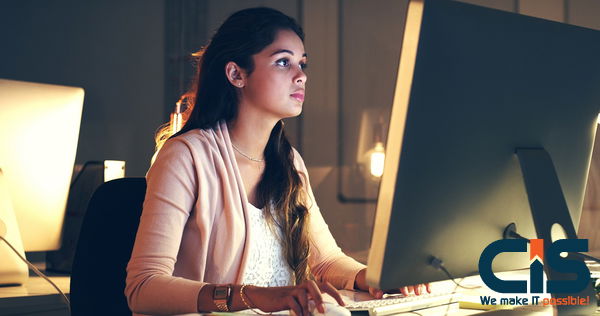
The right approach to maintenance is an essential decision that organizations must make because it directly impacts the reliability and efficiency of assets, operations, and their performance. Choosing a maintenance strategy that aligns with an organization's objectives, support, resources and specific industry requirements is essential. How to choose the best maintenance method for you:
- Define Maintenance Objectives: Begin by clearly defining your maintenance goals and objectives. What do you hope to accomplish with your maintenance? Some examples include decreasing downtime, increasing asset reliability, minimizing costs, enhancing the safety of your employees, and complying with regulations.
- Asset Assessment: Identify and classify your assets according to their importance for your business. If they are not functioning correctly, critical assets can have an even more significant impact on your company. Safety implications, production disruptions, and financial effects are all factors to consider.
- Different Maintenance Methods: Familiarize yourself with the other maintenance methods, such as reactive maintenance, pre-emptive maintenance, predictive maintenance, and reliability-centered (RCM) maintenance.
- Resources Evaluation: Assess the available resources for maintenance, such as personnel, budget, and equipment. Make sure you have enough resources to implement your maintenance strategy.
- Asset Complexity: Take into account the complexity of assets. Specific equipment and infrastructures may need specialized maintenance methods or specialist knowledge. Check if your company has the necessary expertise to perform specific maintenance techniques.
- Technology and Data: Evaluate your data collection capabilities. Data and technology are essential to maintenance approaches such as condition-based and predictive maintenance. Make sure you have all the infrastructure necessary for data-driven management.
- Compliance with Regulations: Consult industry standards and regulations that could dictate your maintenance methods. Ensure that the maintenance method you choose aligns with these standards to avoid compliance issues.
Conduct a Risk Assessment
- Cost Benefit Analysis: Complete a cost-benefit analysis of each approach to maintenance. Consider the cost of installation, ongoing maintenance costs, potential downtime, and expected benefits in terms of decreased failures and improved efficiency. Comparing the cost-effectiveness over time of each method.
- Expert Consultation: Seek the input of maintenance professionals, engineering experts, and industry experts. They can offer valuable insights on how to maintain your equipment.
- Customizing the Approach: In most cases, organizations use various maintenance methods. Be sure to tailor your maintenance approach for each asset. Predictive or condition-based preventive maintenance may be used for critical assets. In contrast, a more proactive approach may be taken with less important ones.
- Monitoring and adaptation: Once a maintenance strategy has been selected, monitor it continuously to ensure its efficacy. Prepare to adjust and fine-tune your maintenance approach in response to performance data or changing conditions.
- Documentation & Training: Document your maintenance procedures and schedules. Ensure the maintenance team understands its role in implementing your chosen strategy.
When choosing the best maintenance strategy, it is essential to consider organizational goals, assets' criticality, resources available, the complexity of assets, data capability, regulations, and cost-effectiveness. Organizations can achieve maintenance goals, improve asset performance, and reduce downtime using a systematized approach when choosing the best maintenance strategy. It is important to remember that selecting a maintenance strategy does not have to be a single decision but instead reflects evaluating and adapting the approach over time.
This Will Help You Implement Your Maintenance Strategy
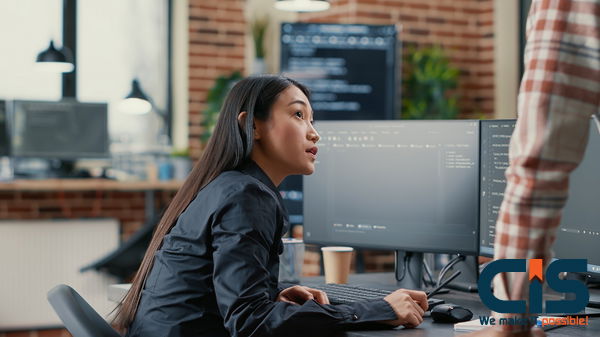
It is essential to implement a strategy for maintenance that will ensure the longevity, reliability, and availability of your assets. These are critical steps for implementing your maintenance strategy successfully:
Create a Maintenance Team
A skilled team of maintenance technicians is essential to a successful implementation. Hire and train maintenance technicians to implement your strategy. Take into consideration the following:
- Hiring: Employ individuals with the appropriate skills and experience to do the job. Search for relevant certifications and training.
- Training: Offer ongoing training to your staff and provide development opportunities.
- Cross Training: Train your technicians in multiple maintenance disciplines to increase their versatility.
Establish Standard Operating Procedures (SOPs)
Standardized and transparent procedures are crucial for consistent maintenance. Document and develop SOPs to cover all tasks. The courses must include safety measures, step-by-step directions, and troubleshooting guidelines.
Select Maintenance Management Software
Implementing specialized software for maintenance management or a Computerized Maintenance Management System is advisable. These tools streamline maintenance, provide insight into efficiency and performance, and track data about assets. Maintenance software should have the following features:
- Maintenance Work Orders: Manage and create work orders.
- Asset tracking: Maintain detailed records on asset histories and maintenance activities.
- Inventory management: Manage the spare parts and consumables in your inventory.
- Performance reporting: Create reports and analytics for evaluating the effectiveness of maintenance strategies.
Define Key Performance Indicators (Kpis)
Key Performance Indicators are a great way to gauge the success of your strategy. Some common KPIs are:
- Mean time between failures (MTBF). Measures the average amount of time that equipment fails.
- Mean time to Repair (MTTR) measures the average amount of time required to repair equipment.
- The Overall Equipment Effectiveness Evaluation (OEE) evaluates the efficiency of assets.
Monitor KPIs to identify improvement areas and provide a base for making decisions.
Budget for Maintenance
Budget and allocate resources for maintenance. Materials, labor, tools, and technology costs are essential when executing your strategy. Budgeting properly ensures you can address your maintenance requirements without being financially constrained.
Training and Education for Employees
All employees should be educated, and not only the team responsible for maintenance, on the importance of maintaining equipment and their role in supporting the strategic plan. Encourage a culture that encourages ownership and accountability for the care of equipment. Employees who understand the importance of maintaining equipment are more likely than others to be involved in its success.
Safety and Compliance
All maintenance operations should comply with industry and safety standards. All maintenance activities should prioritize safety. Safety protocols should be developed, protective equipment provided, and regular audits of safety practices conducted.
Continuous Improvement
The best maintenance strategies are dynamic, and they're constantly improving. How do you optimize and maintain your maintenance strategy?
- Data collection and analysis: Collect and analyze data collected from equipment sensors and maintenance activities. This data can be analyzed to help you make better decisions.
- Feedback loops: Create mechanisms to collect feedback from technicians, stakeholders, and others. This feedback can be used to improve your strategy.
- Conduct Root Cause Analysis: If equipment fails, perform root cause analysis to determine the underlying problems and prevent further failures.
- Refine and Adjust: You should be prepared to refine and adjust your maintenance strategies based on new technologies and the lessons you have learned in experience.
- Benchmarking - Compare your maintenance performance with industry benchmarks to find areas of improvement.
Designing A Maintenance Strategy That Reduces Downtime
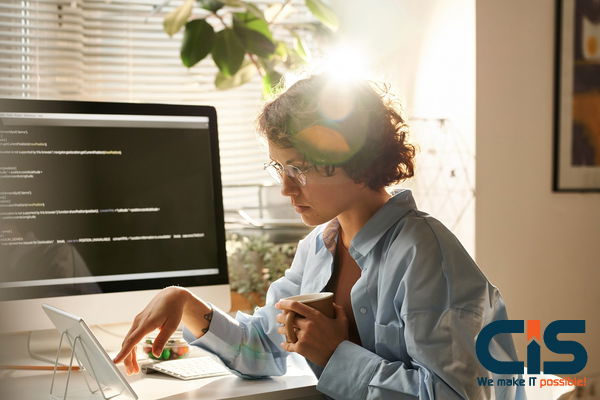
It is vital for companies that depend on equipment or machinery to function efficiently to develop a maintenance strategy. The cost of downtime in lost revenue, production, and customer satisfaction can be high. These steps will help you create a plan to minimize downtime.
- Asset Criticality Analysis: Start by categorizing and identifying your assets according to their importance for your business. If they are not working correctly, critical assets can have an even more significant impact on your company. When determining the criticality of an asset, consider factors like safety, interruptions in production, financial implications, and environmental impacts.
- Define maintenance objectives:Define your goals for maintenance and the reduction of downtime. Decide what downtime goals you wish to accomplish, for example, reducing downtime unscheduled by a specific percentage or improving asset availability.
- Monitor and collect data: You need accurate information on your equipment's condition to reduce downtime. Install a monitoring system that collects data on your equipment. This may include sensors and health checks.
- Set Alarms and Thresholds: Set thresholds for alarms and amplifications of data. The points determine when the equipment has deviated from its normal operating condition. When entries are reached, alarms will trigger maintenance actions. This allows you to fix issues before there is downtime.
- Create Predictive Maintenance models: Use predictive maintenance models to find patterns in data. Artificial intelligence and machine learning can predict maintenance requirements accurately. This allows you to plan maintenance at the most cost-effective time.
- Prioritize maintenance tasks: Prioritize maintenance tasks using your data and criticality analysis. Concentrate on assets that are critical and show signs of imminent failure. Allocate resources to where they're needed the most.
- Optimise Spare Parts management: Make sure you maintain an adequately organized inventory of critical parts and spares. Install an inventory management system that tracks usage and reordering points. This will ensure the correct details are available at all times. It helps to minimize the downtime caused by waiting for parts.
- Documentation and communication of procedures: Standardize and document maintenance procedures. To ensure consistent execution, communicate these procedures to the maintenance team. Documentation should include troubleshooting and safety tips.
- Embrace Technology: Automate the collection of data and its analysis by using technology such as IoT sensors and predictive maintenance software. These tools can provide real-time insights into equipment health and trigger alerts if there are issues.
- Evaluation and adjustment of your evaluations is a regular process: Continuous improvement is essential. Analyze downtime and performance metrics to evaluate your strategy regularly. As circumstances change and lessons are learned, adjust your plan accordingly.
- Employee Training: Spend money on training your team to equip them with the knowledge and skills to implement your strategy effectively. You can reduce your downtime and improve the reliability of equipment and infrastructure by following these simple steps, monitoring your strategy, and continually adapting it. The proactive approach will reduce costs, increase productivity, and improve customer satisfaction.
- Root Cause Analysis (RCA ): Root cause analysis is an excellent way to determine the causes of unexpected downtime. You can take corrective measures to prevent future equipment issues by understanding why failures occur. RCA can be a powerful tool to improve continuously.
- FMEA (Failure Mode and Effects Analyses) ): FMEA systematically identifies failure modes, their effects, and potential consequences of critical equipment. This proactive approach will allow you to prioritize maintenance tasks and allocate resources to where they are needed most to avoid downtime.
- Regular inspections and audits: Inspect and audit equipment to identify early warning signs such as wear or deterioration. By taking proactive steps, you can address problems before they become more severe and cause unexpected downtime.
- Prepare an Emergency Plan Create and share an emergency plan outlining the actions to be taken in case of unplanned downtime. A well-defined downtime plan can reduce this impact on your operations and minimize its duration.
- Condition Monitoring Technology: Utilize advanced monitoring technologies such as oil analysis, vibration analysis, thermography, and ultrasound. These tools provide real-time data on the equipment's health, allowing for early detection and maintenance prediction.
Backup And Redundancy Systems
Redundancy is essential for the critical equipment. If one system or component fails, the backup will take immediate control, which reduces or eliminates downtime.
- Train the Operator: Equipment operators should be trained to identify and report any anomalies or signs that equipment is malfunctioning. The operators are the first to identify problems and can help minimize downtime.
- Monitor your home or office remotely with continuous monitoring: Use remote access and continuous monitoring capabilities. The technologies allow maintenance teams to remotely access diagnostics and equipment data, allowing quicker responses and reducing the physical presence requirement at the site.
- Benchmarking and best practices: Compare your performance in maintenance to industry best practices and standards. Compare your metrics for downtime to the industry averages, and you can get a better idea of where improvement is needed.
- Plan and schedule your work: Plan and schedule maintenance in advance to maximize efficiency. Plan maintenance activities during planned downtime when production will not be critical.
- Vendor-supplier relationships: Keep strong working relationships with suppliers and equipment vendors. Reduce downtime by ensuring quick access to spares, technical assistance, and supplier expertise.
- Continuous Communication: Encourage open communication between your team members and departments. Encourage the collaboration of all departments and information sharing related to maintenance and equipment performance.
- Celebrating Success and Learning from Failures Celebrate and recognize the success of your efforts to reduce downtime. It is also essential to learn from any failures or unplanned downtime. Perform post-mortem analysis to determine areas of improvement and corrective action.
- Executive Support and Investment: Reduce downtime by securing executive investment and support. The financial benefit of reduced downtime can be used to justify the budget and resources for maintenance improvement. You can improve your ability to optimize your operations, reduce downtime, and increase asset reliability by incorporating additional maintenance strategies. Downtime reduction requires commitment, continual improvement, and proactive maintenance.
Want More Information About Our Services? Talk to Our Consultants!
Conclusion
An effective maintenance strategy will help you achieve operational excellence. Following the guidelines in this guide will help organizations minimize downtime and costs, improve safety, and increase the reliability of assets over the long term. Maintenance is not a one-time task but a commitment to continuous excellence.
Remember, as you begin this journey, adaptability and continual improvement will be critical to the success of your maintenance strategy. Begin by setting goals, prioritizing your assets, choosing the best maintenance method, implementing your system, and continuously refining and optimizing it. Your organization will achieve higher efficiency and reliability with a solid maintenance strategy.