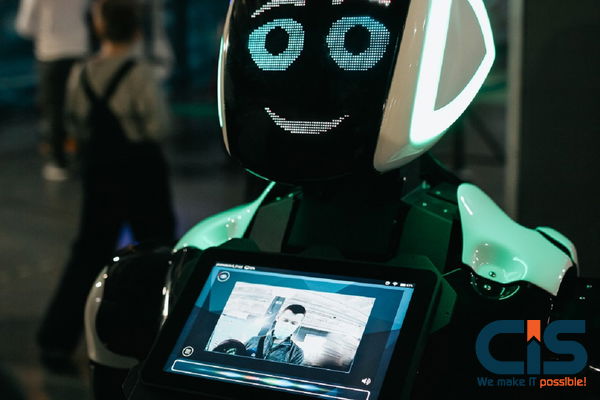
This generally includes improving lead times and quality, super productivity, and inventory project management. These require effective communication across all levels and departments.
ERP solutions for beverage manufacturers have proven to improve workflow visibility, streamline asset project management, and provide real-time reports that support data-driven decision-making. Many modern companies favor manufacturing ERP implementation to stay competitive.
Stakeholders should consider the role of ERP vendors in manufacturing companies when deciding on an ERP vendor.
Five ERP Selection Criteria For Manufacturers
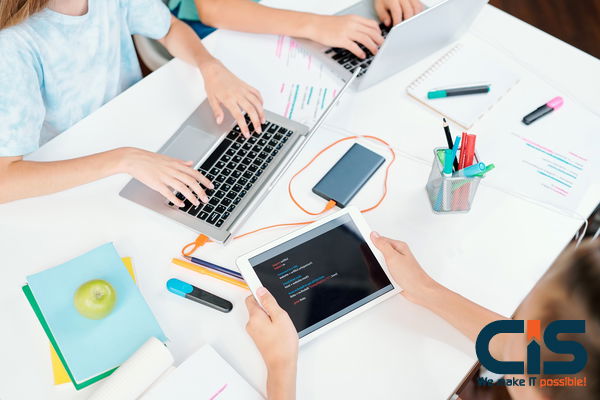
Functionality is the best criterion for ERP selection, and it's rightfully so. However, feature sets can often be identical when it comes to ERP platforms that are specific to an industry. Stakeholders need to be aware of other important aspects when evaluating ERPs.
1. The Deployment Model
There are fundamental differences between cloud solutions and on-premises ERPs, including pricing models, maintenance requirements, and security levels.
On-premises ERP is installed and managed within an enterprise's IT infrastructure. This gives owners full control over the operation of their ERP and allows them to configure, customize and protect it as they wish. However, this requires the IT department to manage all aspects of the ERP system.
Many manufacturers choose cloud-based services ERPs because they have unlimited storage, flexibility, and mobility. These ERPs are flexible and can be customized on demand. They are also accessible from any device at any time. However, public cloud infrastructure providers are vulnerable to hacking and downtime.
Forward-thinking manufacturers can use hybrid ERPs that combine on-premises and online features. You can keep your most sensitive data and operations on-premises while hosting less critical business processes in the cloud technology company. This allows you to tailor the infrastructure to suit your financial needs and offers the best of both worlds.
2. Scalability
Scalability refers to the ability of an IT infrastructure to scale up and how much it will cost. It also includes what maintenance it will need. It would help if you also considered the ease of customization and integration. Do new features require development, or can they be used plug and play?
It is important to select an ERP that allows for global growth and complies with international legal and financial requirements.
Last but not least: If an ERP vendor isn't keeping up with the latest trends, your enterprise may outgrow its ERP capabilities.
3. Integration is Easy
To reap the benefits of an ERP, it must be integrated with your existing manufacturing IT infrastructure.
Depending on the ERP's default features, integration can be done with the default APIs or dedicated tools. Integration through these tools would still require manual work, but this task is achievable for IT departments.
Specialized Manufacturers will need to create an integrated application or adapter for each ERP integration if a platform does not offer one. This situation may require specialist expertise and can prove to be lengthy.
An alternative, more specific option for integration is the in-built EDI connectors or integration modules. These are commonly used in manufacturing to exchange business documents with customers and suppliers.
4. Mobile Application
Reporting and access to real-time data are essential due to the increasing geographical distribution of manufacturing operations. When deciding on an ERP platform for the future, consider its mobile capabilities and whether they meet your needs.
It is important to note that ERP apps may have different features, customization options, and compatibility than their desktop counterparts.
5. The Total Cost of Ownership
Future adopters should consider the ERP price, but in reality, the total cost of an ERP system is often much higher than initially anticipated.
Manufacturers must also make allowances for hardware and user licenses and the necessary implementation, customization, and data migration resources.
It is important to consider operating costs such as additional licenses, support and admin fees, and additional integrations.
Assess the skills of your IT staff in ERP maintenance, customization, and upscaling. Are your IT specialists capable of keeping the system running, preventing downtimes and security problems, and ensuring it is always available? Or will they need additional help or outsource the job to outside ERP developers? External assistance costs can vary greatly from one solution to another and should be considered along with the risks associated with IT outsourcing.
Other concerns not easily overlooked in the marketplace include managing rising demand, sudden fluctuations in order, and supply chain-related issues. Many manufacturing companies install ERP software products to help them manage their operations. They still need to rely on different vendors for various processes throughout their manufacturing life-cycle.
Manufacturing ERP software, an alternative to traditional methods, allows all manufacturing processes to be managed using one optimized solution. It caters to each organization's unique business needs and can transform the manufacturing process.
The question remains: How can Manufacturing ERP software manage demand chains?
Manufacturing ERP Software can be Used to Modify the Manufacturing Business Process.
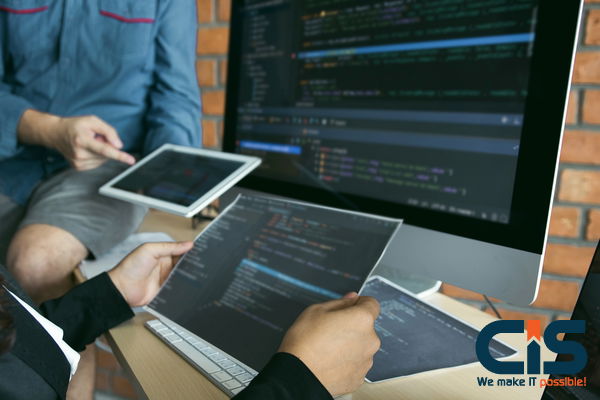
Effective Inventory Management
- Encompasses products and materials are essentials in the Inventory segment, wherein product inventory comprises a bunch of products produced via the manufacturing process cycle of how they are delivered/transported to the clients.
- Management materials can be described as attached strings that must be taken care of. This ensures that the manufacturing enterprise has the right materials in the correct quantities to complete the manufacturing process. It can also cause chaos if two systems are not compatible.
- Manufacturing ERP software can automate vital processes such as BOM (billing of materials), excess inventory management programs, and materials tracking. Some SMEs find that updating all these processes requires manual labor, which can lead to human error.
- Manufacturing ERP software, on the other hand, can reduce human error and automate inventory requirements. It also ensures that material arrives when it is needed.
Preparing Customer's Demand for Satisfaction
- When data is being gathered manually, it is impossible to know what inventory levels are needed from one quarter to the next year. While the forecasting department may be able to make an educated guess based on previous data, it does not account for actual market changes.
- The Manufacturing ERP software will notify you of customer demand shifts using past and current data. This makes forecasting future customer needs easy and simple. It is also more reliable than manual/laborious methods.
No-hassle Collaboration Between Customers and Suppliers
- Manufacturing ERP software (enterprise planning) can streamline business processes and improve response times. Providers of enterprise software can be used to enhance internal communication between all departments and all suppliers.
- This eventually shows a positive effect on collaboration between all stakeholders with effective cooperation, translating challenges into goals and meeting deadlines. Manufacturing ERP software allows for quick and adequate responses to changes. It can be used to expand customer relationships and improve business growth operations.
Increased Productivity for Employees
- We all know that organizations that still use manual processes for manufacturing have higher labor costs than those that automate their operations.
- ERP software can help organizations streamline their processes so that they can spend more time on activities that offer higher returns.
Reduce Processing Time with Ease
- Excess leads to waste in production without any client value. Simple workflows and chains can lead to over-processing, which can cause delays in production or distribution.
- The Latest Manufacturing ERP software helps manufacturing organizations avoid overproduction and directs them toward creating genuine customer value. ERP confirms that manufacturing production meets customer goals using the correct key performance indicators (KPI).
Significant Human Resource Operations
- A training and attendance tracking module can improve the productivity of your manufacturing business. Combining Manufacturing ERP software with HRMS can allow you to combine both. Your firm could automate many paper-based administrative tasks within the Human section.
- Software planning for enterprises can be integrated with third-party business software solutions to simplify the business process.
- Manufacturing organizations must use all available tools to increase efficiency and stay ahead of the demand curve.
Supply Chain with Automation's Charm
- Integrating ERP and supply chain modules effectively can improve communication between suppliers and manufacturers. Human errors can be a major stumbling block in quality issues. Automation of several processes using Manufacturing ERP software can reduce the chances of errors in complex supply chains.
High-Quality Product Quality
- Quality control and quality risk management are vital in manufacturing. Manufacturing ERP software can help businesses monitor their production quality and spot any problems quickly.
Simplified Legal and Regulatory Modifications
- The term regulatory is constantly changing in an organization. Implementing Manufacturing ERP software can avoid any changes that could jeopardize manufacturing processes.
- This can save you money and help you comply with regulations. You can contact an industry specialist to make the necessary changes to meet the evolving regulatory frameworks.
Read More: Top ERP Software & Tools in 2023
Current Supply Chain Crunch Caused by Factors
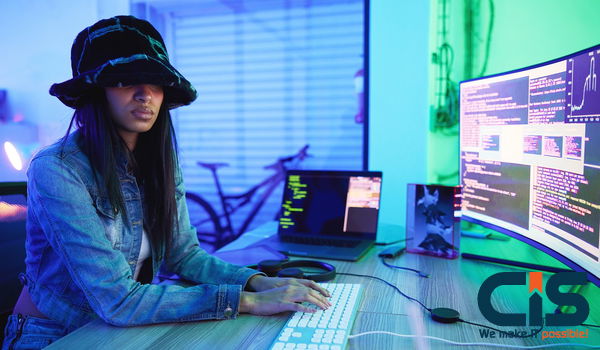
Supply chains are a complex network of stakeholders, including suppliers, partners, distributors, customers, and third-party logistics providers. They include warehouse operations, transport service providers, financial institutions, retailers, and e-commerce websites. An essential component is a supply chain that can adapt to fluctuations in demand.
The escalating effect of COVID (Corruption of International Trade in Imports) on global markets has caused severe disruption to the flow of goods between countries and continents. The current supply chain crisis is not caused solely by the pandemic. These are just a few contributing factors to the existing supply chain crunch.
Trade Policies Changing
Many industries have been affected by the recent rise in import tariffs that government agencies worldwide have imposed. Global trade patterns are rapidly changing. Companies face increased costs and uncertainty when dealing with foreign partners.
Rising Raw Materials and Energy Prices
Oil producers have been hard hit by rising crude oil prices. The trend is expected to continue through 2023, as there has been a sharp increase in mining costs. Transport infrastructure is also being affected by rising fuel prices. Moreover, increasing natural gas prices will likely cause additional costs for power generation facilities.
Are you Ready to Find your Best Fit?
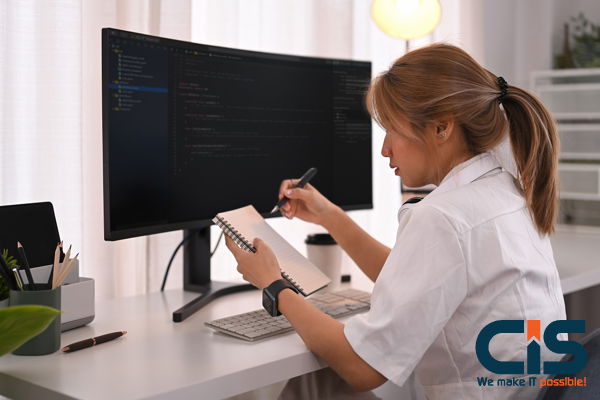
Our "BEST FIT" tool matches top ERP Systems for your business.
Increased Input Costs
In 2022, raw material costs will increase and continue to rise through 2023. With the pandemic in many countries and the rising cost of raw materials, this trend is not slowing down. The rise in energy and input procurement costs for agricultural commodities such as corn and soybeans is a large part of this increase. Over the past 12 months, production costs for other materials like plastics and metals have also increased.
E-commerce Platforms are Being Adopted More Frequently
It's impossible to hide behind physical distribution centers outside China with the fast-paced adoption of online shopping platforms like Amazon and Alibaba. It is now even more difficult for manufacturers to move products worldwide from factories into retail shops. Manufacturers must look for new cloud-based software solutions to the adaptable supply chain crisis due to the shift in demand dynamics.
Five Ways an ERP System Can Help Reduce Supply Chain Disruption
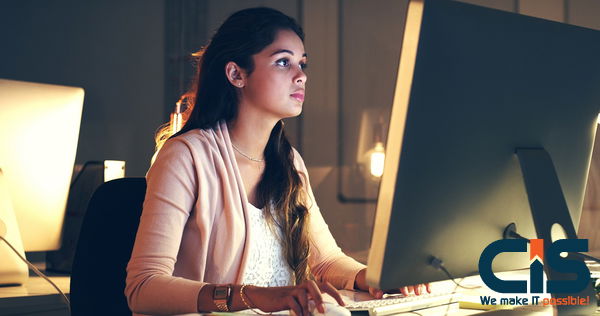
To survive disruptions and ensure smooth trade operations following the pandemic, companies must invest in the broader supply chains of the future. This means using the right technology business management software solutions, such as ERP software. These are the top five ways that ERP software can improve supply chain management.
Better Inventory Management
ERP-based inventory management solutions give visibility to every part of your supply chain industry. An ERP offers businesses access to suppliers, customers, distributors, and partners. This allows them to track inventory status and plan shipment accordingly. The best SCM tools will enable you to track orders and shipment statuses, improve forecast accuracy and optimize warehouse delivery times and fulfillment schedules. The critical data that shows how much inventory is required to meet current demand and forecasted requirements enhances the accuracy of inventory management programs.
Distribution ERP has integrated inventory tracking capabilities. This includes dynamic replenishment methods, inventory analytics, and inventory tracking. This allows for quick identification of low products, comparing actual inventories with sales forecasts.
Streamline Purchasing Processes
ERP software can be used by businesses to manage all aspects related to material and product procurement. This includes vendor selection, contract negotiation and purchase requisitions, payments, inventory tracking, and order processing. These processes can be streamlined to reduce manual tasks, make it easier for staff to work on higher-value projects, save money, and avoid costly mistakes. Distribution ERP has integrated inventory tracking capabilities. This includes dynamic replenishment methods, inventory analytics, and solution software monitoring. This allows for quick identification of low products, comparing sales forecasts with actual inventories.
Complex Supply Chain Networks: Effective Management
Many distributors and manufacturers rely heavily upon third-party service providers (like freight brokers, shippers, and carriers), who play an integral part in their logistics and operations. Many service providers lack integrated operating systems, making it difficult for companies to see each component of their supply chain field. This is a problem for many companies. These different elements can be easily interconnected with an ERP system. These interactions are recorded into a central database so businesses can access data reporting to analyze key metrics like landing costs, cycle counts, and warehouse activities.
Higher Customer Service Levels
Poorly planned distribution networks can cause delays in shipment, which, in turn, reduces customer satisfaction. Customers don't receive accurate estimates of delivery times, which can lead to more problems. If this happens, customers may complain about poor service and decide not to do business with you again. Online reporting tools can be built with an ERP solution that provides real-time visibility of shipment status. The integrated warehouse management software helps you optimize storage space based on forecasted demand.
Integration of Internal Business Processes
An ERP system of the highest quality management integrates seamlessly with other enterprise software. Invoicing is an example of a common interface between ERP systems for manufacturing and accounting software. An ERP solution allows you to generate invoices automatically from sales orders and then send them to customers or vendors. Automated payment receipt and refund processing are possible.
These uncertain times require the most effective business application solutions for companies. A well-designed ERP system can help lead manufacturing and distribution companies through the current supply chain crisis in 2021 and 2022. These systems can also ensure strategic growth over the years ahead when market forces will be more predictable. Although there is little you can do about the causes of the supply chain pain points, ERP systems offer proven software solutions that allow you to overcome the current storm and navigate through it.
Bottom Line:
It is much easier to bring transformation within an organization than in the past. To stay competitive in a highly competitive market, implement Manufacturing ERP software. Manufacturing organizations must use all available tools to increase efficiency and stay ahead of the demand curve.
Manufacturers are now more focused on making their production processes cost-effective, flexible, and resilient to disruptions in the modern world. Originally designed to support manufacturing workflows, ERPs are a good solution for reaching these goals. They also streamline some labor-intensive tasks and provide useful operational insights.
Manufacturers must consider other aspects of ERP software relevant beyond functionality to make cloud-based ERP software more cost-effective, including the available hosting options, the total cost of ownership, and ease of integration and scaling.