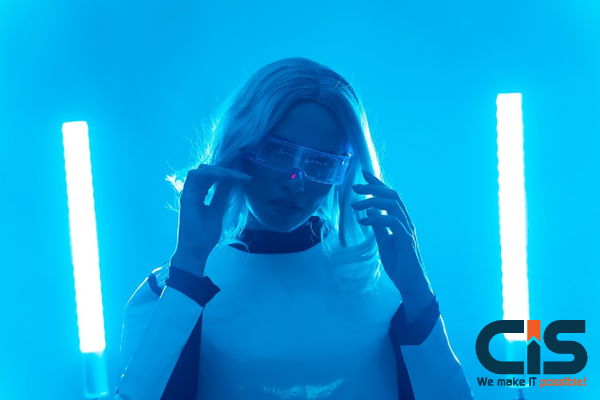
The idea of "smart manufacturing" is broad. It cannot be applied straight to a production line. A "smart manufacturing" ecosystem is a collection of several technologies and approaches that, when used together, can be referred to as smart manufacturing. These so-called "enabler" technologies and solutions aid in streamlining the production process and boosting total revenue.
Several of the most prominent market enablers are:
- Artificial intelligence
- Blockchain in manufacturing
- The industrial internet of things
- Robotics
- Condition monitoring
- Cyber security
Companies are always looking for ways to reap the benefits of enablers. When we look closely at enablers, we see that they either generate or accept data. Or both. Data analysis can help make the production process more transparent, efficient, and flexible.
What is Smart Manufacturing?
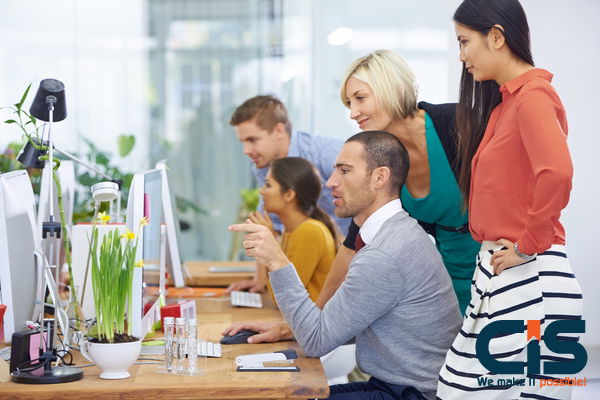
Process plants can't compete in a more complex market without full control and visibility over all aspects of production and operations. Smart manufacturing is essential for plants to adapt to changing market conditions, business contexts and increasing standards of safety, quality and environmental impact. Process plants can be smartly manufactured with smart manufacturing.
- Optimize processes with data.
- With real-time granular data analysis, you can see every corner of your plant, including processes, resources and assets.
- Safety for workers and the wider environment
- They will be more flexible, allowing them to react to customer requests for customization and small quantities and pivot better in a crisis.
- Accelerate innovation and accelerate time to market.
- Reduce waste by moving physical tests online to simulate the results and decrease energy consumption.
The adoption of smart manufacturing is an example of this. Based on quick growth and smart manufacturing, a 12.4% CAGR is anticipated until 2024. According to a recent survey, 85% of business executives agree or strongly agree, investment in smart factories will increase.
How Can Process Plants Use Smart Manufacturing?
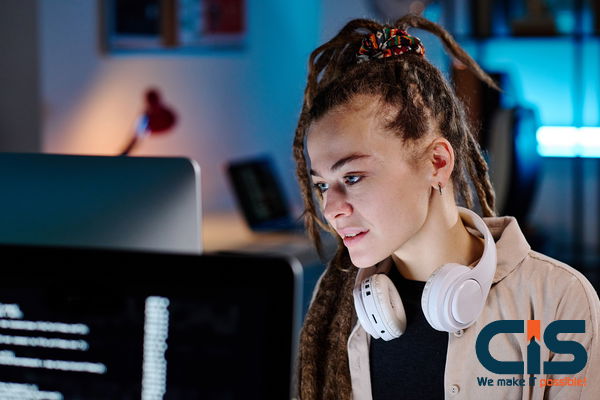
Advance Digitization
Smart manufacturing is based on integrated digital processes. Therefore, it is important to first ensure that all analogue or manually run processes are digitized.
Improve Data Management
Big data is the foundation for A.I./ML-powered systems and smart manufacturing. You must assess your data storage and data-capturing methods for ML algorithms to offer reliable predictions.
Create A Smart Manufacturing Culture
Digital transformation is extending to smart manufacturing. The success of a digital transition depends on digital culture, as is widely acknowledged. Ensure your staff knows the advantages and needs of a smart factory. Retrain or add talent to increase your skills. Finally, make sure you support and get the buy-in from management.
Connect Networks To Processes
Process plants often implement digital tools and projects in an irrational, isolated manner, depending on the area of greatest value and need. Smart manufacturing involves connecting individual assets and systems to form a single network.
Attention to Cybersecurity
While smart factories can be a boon for plants, they also have the potential to increase your attack surface and expose security vulnerabilities. To avoid your plant being vulnerable to hackers, it is important to constantly test your perimeter defenses.
What Makes Smart Manufacturing More Competitive For Process Plants?
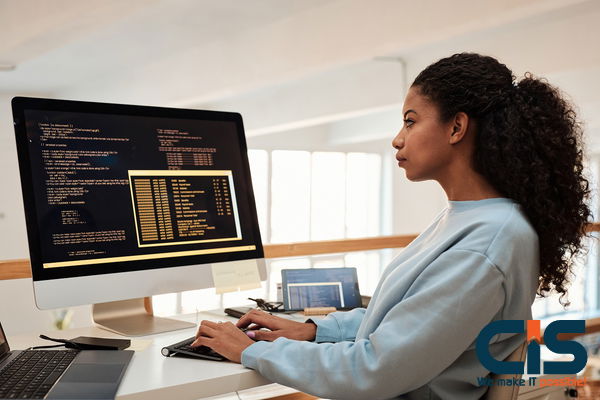
Smart manufacturing allows process plants to be more flexible and innovative while reducing costs, waste, and quality, improving safety and environmental regulations. Smart manufacturing allows process plants to be more proactive in their business growth strategies and improve their ability to deal with unexpected events, such as changes in customer demand or broken supply chains.
How Data Drives Smart Manufacturing
All that data can do is enable smart production. Data will inform us of the best time and method to take. The danger of implementing these enablers must be considered. The three categories of businesses that make up smart manufacturing's stakeholders are "Product and Control Solution Providers," "I.T. Solution Providers or Enablers," and "Connectivity Solution Providers."
- All companies involved in developing and maintaining automation products or services are included.
- Enables power and provides manufacturing It solutions for the entire concept of IIoT. They assist in the monitoring, construction of control, and analytics infrastructures.
- A connectivity solution provider is a telecom service provider that allows for the seamless data flow to support asset management.
Implementation of IIoT
The industrial internet of things (IIoT) is a network that utilizes data communication methods to link every machine, device, and/or process. All machinery and industrial equipment is linked to sensors that produce pertinent data. This data transfer to the cloud or software system is made possible by data communication systems. The enormous volume of data can offer a wealth of information that, when analyzed, may reveal weak points in the manufacturing process. The production systems then collect the data as feedback for corrective measures.
Smart manufacturing has huge potential for IIoT. There are production limits, so how can you increase profits? Because there isn't demand, you can't increase production. You need to examine the backend of your production process and optimize it. This is only possible if you know the details of your production process. This is where IIoT enters the picture. You can use sensor-generated data to monitor production processes and analyze the data to take corrective actions to improve efficiency and profitability.
Implementing IIoT within existing or old organizations is difficult, but it can be done in new manufacturing facilities. Because smart manufacturing concepts must be implemented right from the beginning of a manufacturing facility's design, this will ensure that the best results are achieved. Although smart manufacturing isn't widely used, it is being implemented in a few instances in certain organizations. You can't make any changes to the factory design or machine layout to implement the sensors and related technology. Implementing IoT in an existing or older manufacturing facility is sometimes difficult.
The IoT market for manufacturing will expand from USD 12.67 billion to USD 45.30 billion at a compound annual growth rate (CAGR of 29.0%). The growing demand for central monitoring and predictive maintenance of manufacturing equipment are major drivers of IoT in the manufacturing market. Market growth is expected to be driven by the increasing demand for operational efficiency, agile production, and control, as well as a demand-driven supply chain and related logistics.
Artificial Intelligence Is Increasing In Manufacturing
Although artificial intelligence is an old concept, it is finding its applications in manufacturing. The last five to six years have seen a significant increase in investment and interest in artificial intelligence in manufacturing. This is due to several reasons. A.I. can only work if there is enough data available. It has been difficult to develop the necessary capability.
- Low-cost sensors can generate huge amounts of data
- Store data in low-cost systems
- Data processing at reasonable rates
They have made it possible to implement A.I. in manufacturing shops. In the past, manufacturing was done in low-cost countries. It was difficult for them to justify their manufacturing systems' high costs of A.I. implementation. However, it's now possible to implement A.I. in countries, the factory of all things, due to increased wages. Significantly invested in artificial intelligence solutions, especially in manufacturing and related applications.
Robots with A.I. capabilities are also being used in manufacturing ecosystems. Using robotics with A.I. capabilities allowed for perception-based decision-making that was otherwise impossible to achieve using rule-based algorithms in robots. Another important area where A.I. is useful is predictive maintenance. Predictive maintenance allows predicting performance, breakdown, and operating conditions on equipment or machines in real time.
Manufacturing's artificial intelligence (A.I.) market will increase from USD 272.5 million to USD 4,882.9 million in 2023 at a CAGR of 52.42%. The widespread use of robotics and computer vision in manufacturing, cross-industry alliances and collaborations, and large increases in venture capital investments will all contribute to the expansion of A.I. in this sector.
Blockchain in Manufacturing: The Future
Manufacturing with blockchain is still in its infancy. It is a technique that is heavily debated in manufacturing environments, though. Currently, financial systems take advantage of it. Companies are looking into how it may be used in manufacturing, though.
Blockchain technology could greatly impact the future of many industries, including aviation, food and medical, beverage, and healthcare. Due to strict regulations and rules, these industries must scrutinize their suppliers throughout the value chain. Blockchain could be used to maintain quality control when raw materials are developed. Blockchain development to support supply chain functions across manufacturing ecosystems is the focus of most attention.
Read More: Smart Manufacturing: What is it?
The following industries are developing blockchain: apparel, agriculture, transportation, fertilizer, aviation, healthcare, and solar energy. This list isn't exhaustive, and as blockchain technology matures, more industries can implement it. Although the blockchain market in manufacturing is still being conceptualized, we expect it to generate significant revenue starting in 2023. Numerous businesses have started investigating and investing in blockchain technology's potential advantages in industrial ecosystems.
Industrial Robotics: Their Importance
Implementing industrial robots is the next step that will make a manufacturing plant smart. Industrial robots are not a new concept. They have been around for 40-50 years. The only thing that has changed in industrial robots' lives is their ability to become intelligent. The robots had been programmed to perform one task at a given time. You must modify the codes to perform other types of tasks.
Robots can now be connected to the sensor network on the production floor. They receive data from the sensors and adjust their actions accordingly. Robotic systems are slowly incorporating artificial intelligence, which makes them autonomous. Robotic systems can adapt to changing situations via artificial intelligence (A.I.). Businesses hiring AI software development companies for the same.
Asia-Pacific is where the majority of industrial robots that are now in use are found. The use of industrial robots is essential to the automotive sector. One of the main forces behind the development and expansion of robots is the government initiative. China and the USA are providing the necessary push to increase robotics demand.
Collaborative robots are a new breed of robots that are starting to appear. These robots can support all human work and work alongside humans. For instance, a collaborative robot can observe what an operator on an assembly line is doing and pick up the duty from him. The identical task is then carried out by the robot on its own with the same level of accuracy. Regarding application, collaborative robots have advanced to the point where it is difficult to tell them apart from industrial robots. Collaborative robots, which could previously only handle light work, may now handle larger duties that cannot be handled by industrial robots.
The market for industrial robots will be valued at USD 71.72 Billion by 2023. This is a 9.60% increase over the previous forecast period. By 2023, it is anticipated that the market for collaborative robots will be worth USD 4.28 billion. It will expand at a CAGR of 56.94% from 2017 to 2023. The two key factors driving the industrial robots market are rising automation investment across industries and rising small- and medium-sized company (SME) demand in developing nations.
Digital Twins: The Benefits
Another concept that is part of the ecosystems for smart manufacturing is the digital twin. This creates a virtual model of an asset, process or system using data from sensors within the asset or system. It also uses algorithms to make reasonable projections about the process. Digital twins will be used for predictive maintenance. Digital twins can reduce the time and costs of product development and eliminate unplanned downtime. Digital twin adoption is increasing due to the popularity of IoT, cloud platforms, 3D printing, and 3D simulation software.
Aerospace & defense, automotive & transportation, electronics & machine manufacturing, energy & utility, and electronics & electrical & machine maintenance are the key industries that use digital twins. As the idea of digital twins develops, we might see it employed more frequently in fields like retail and the consumer goods industry.
Smart Factories For A Changing Environment
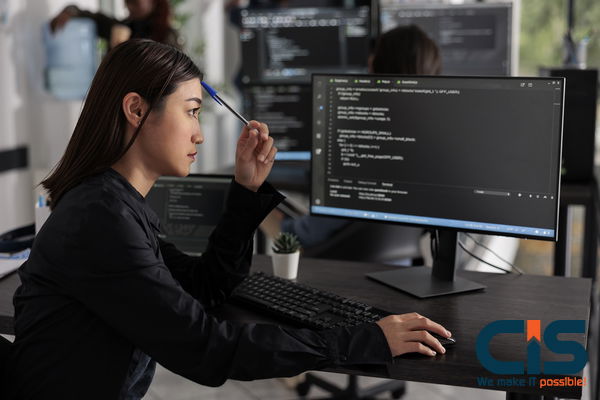
Business leaders have realized that digital transformation has become a top priority for supply chains, manufacturing operations and those who want to remain competitive. Global supply chain weaknesses were further exposed by the pandemic.
The manufacturing sector should already be aware of what COVID-19 has demonstrated, according to a report. As opposed to the conventional supply chains and production ecosystems, we need to transition to digitally enabled, more adaptable, nimble solutions. Smart factory technologies are being developed because of consumer expectations. The Amazon Effect is a trend in which consumers increasingly demand next-day delivery. Entrepreneur magazine reported that the Amazon Effect affects the U.S. and global economies.
Evidence shows that consumers do not anticipate ease in the pressure on e-commerce suppliers to match Amazon's speed and efficiency. Because older systems cannot keep up with the demands of this phenomenon, this tendency is a significant contributor to the rising demand for smart manufacturing technologies.
Read More: What are the Biggest Benefits from Smart Manufacturing Software
What Is The Secret To A Smart Factory?
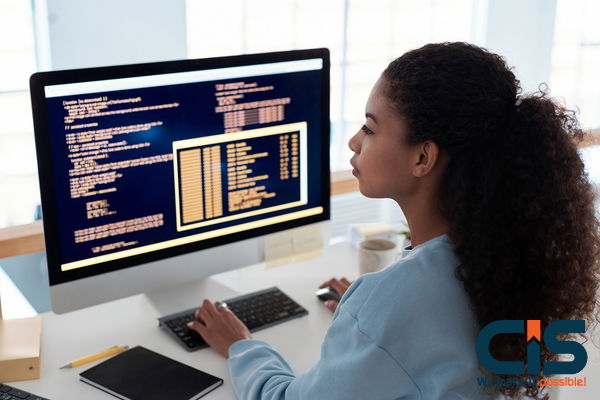
Automated processes are often referred to as unique to smart factories. However, automation and robotics have been used in manufacturing operations for decades. Traditional factories still use automation in many areas, including cameras, barcode scanners, and digitized production equipment.
These devices, however, are not interconnected. Traditional factories have their unique systems that work in isolation. They must all be manually coordinated and integrated. Smart digital factories integrate people, machines and Big Data into one digitally connected ecosystem. Smart factories analyze and curate data and learn from past experiences.
It uses data to interpret and gain insights to predict trends and events and recommends and implements smart manufacturing workflows. To self-correct and optimize, a smart factory continuously improves its processes. It can help humans and themselves become more resilient, productive, and safer. A smart factory's structureThree steps can summarize the basic structure of a smart plant: These are the three major steps that make up a smart manufacturing plant.
-
Data acquisition
Modern database technology and artificial intelligence enable the curation and collection of varied data sets across the supply chain, industry, and globally. New data sets can be created using the Industrial Internet of Things (IIoT), which uses sensors and gateways to enable connected equipment to collect data and input it into the system. AI-powered systems can gather data sets about performance, market trends, and logistics via several data portals.
-
Data analysis Advanced
Analytics and contemporary data management tools are used by machine learning and intelligent business systems to make sense of all the obtained data. IIoT sensors can identify when machines need to be repaired or maintained. Market and operational data can also be gathered to identify possible hazards and opportunities. You can monitor workflow efficiency over time and make adjustments as necessary to maximize it. The readily compared and analyzed data sets provide infinite combinations for supply chain planning and digital manufacturing optimization.
-
Intelligent factory automation
Workflows can be set up, and commands can be delivered to all machines and devices in the system after data gathering and analysis are finished. These gadgets might be found inside the factory's walls or in the supply chain and manufacturing connections. Smart workflows are constantly being optimized and monitored. A news report can alert 3D printer workflows to increase production priority for an item if there is a surge in demand. Inventory buffers may be placed into rotation to eliminate disruption caused by delayed raw material shipment.
Smart Factories Offer Many Benefits
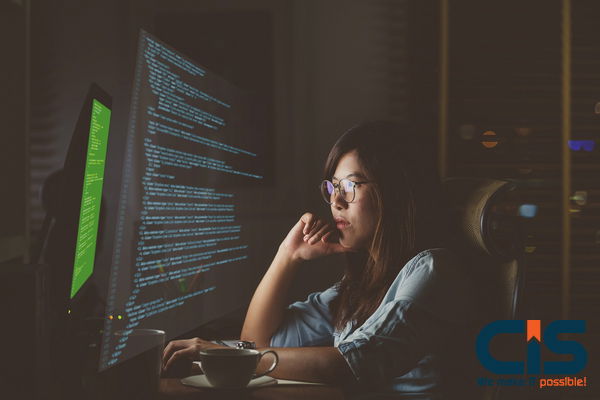
Many businesses have been happy using supply chain management practices and systems that haven't changed much in decades. Supply chain managers must discover solutions that offer significant and demonstrable benefits - and do so fast - as consumer expectations and economic uncertainties rise, only 43% of enterprises have implemented smart factory efforts, 68% of companies implemented smart factory initiatives. Companies that engage in digital transformation or smart industrial solutions reap huge commercial rewards.
-
Productivity & efficiency
Manufacturing has been primarily about reacting to events or trends that have already occurred. The company can then be steered in a different direction. Supply chain management becomes more responsive and resilient due to smart factory technologies that lessen the need to react. Big Data analysis and predictive analytics help find and execute optimized procedures. Efficiency gains from smart manufacturing include just-in-time inventory management and precise demand forecasts.
Thanks to digital insights, those operating in smart factories can streamline their efforts. The productivity of the overall operation is increased as a result. Companies report 12% increases in manufacturing output, utilization, and labor productivity when they invest in smart factory initiatives. Smart factories are expected to outperform traditional ones, with 30% more net labor productivity by 2030.
-
Safety and sustainability
Consumers will pay more for ethically sourced products made using environmentally and socially responsible manufacturing methods. Businesses can now identify opportunities to use smart factory technology to make manufacturing safer, more sustainable, and more responsible.
At any point in the supply chain, the origin and quality of all materials and supplies can be verified by smart factory managers using digital breakthroughs like RFID and blockchain, three of the top occupational injuries can be decreased or completely avoided thanks to robots.
-
Quality and customer experience
Similar to the kid's telephone game, conventional manufacturers struggled to ensure their instructions reached lower-level manufacturers and suppliers in their supply chains. Cloud connectivity is used by the smart factory to offer suggestions and real-time information at all stages of the manufacturing process.
Because of the capacity to swiftly customize and adapt to shifting trends, customers can have items that are always current. System vulnerabilities and possibilities for improvement are readily found through advanced system data analysis. This raises product reviews, increases market competition, and lowers the possibility of costly recalls or returns.
Want More Information About Our Services? Talk to Our Consultants!
Conclusion
Manufacturing facilities may become more flexible and imaginative with smart manufacturing, which also reduces costs and waste and enhances compliance with safety, quality, and environmental laws. Process plants that use smart manufacturing can improve their ability to deal with the unexpected, such as rapid changes in customer demand, faulty supply chains, or a global pandemic, while also taking a more proactive approach to corporate growth strategy.